The Science Behind Porosity: A Comprehensive Guide for Welders and Fabricators
Comprehending the elaborate systems behind porosity in welding is important for welders and producers striving for flawless craftsmanship. From the make-up of the base materials to the ins and outs of the welding procedure itself, a wide variety of variables conspire to either exacerbate or minimize the existence of porosity.
Recognizing Porosity in Welding
FIRST SENTENCE:
Assessment of porosity in welding exposes crucial understandings into the integrity and top quality of the weld joint. Porosity, defined by the presence of dental caries or spaces within the weld steel, is a common concern in welding processes. These voids, otherwise properly dealt with, can endanger the architectural honesty and mechanical properties of the weld, resulting in possible failings in the finished item.

To find and measure porosity, non-destructive screening approaches such as ultrasonic screening or X-ray examination are frequently employed. These methods permit the identification of internal flaws without jeopardizing the integrity of the weld. By analyzing the dimension, form, and circulation of porosity within a weld, welders can make informed decisions to improve their welding procedures and accomplish sounder weld joints.
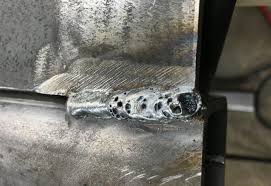
Factors Affecting Porosity Development
The event of porosity in welding is affected by a myriad of factors, ranging from gas securing effectiveness to the ins and outs of welding specification settings. Welding specifications, including voltage, current, travel speed, and electrode type, additionally impact porosity formation. The welding technique used, such as gas steel arc welding (GMAW) or shielded steel arc welding (SMAW), can influence porosity formation due to variants in warm distribution and gas protection - What is Porosity.
Results of Porosity on Weld Quality
Porosity development dramatically endangers the architectural honesty and mechanical buildings of welded joints. When porosity is present in a weld, it creates voids or tooth cavities within the product, decreasing the general stamina of the joint. These spaces act as tension concentration factors, making the weld much more prone to breaking and failure under load. The presence of porosity also deteriorates the weld's resistance to deterioration, as the trapped air or gases within deep spaces can respond with the surrounding atmosphere, resulting in degradation in time. In addition, porosity can impede the weld's capability to withstand stress or influence, more endangering the total top quality and integrity of the welded framework. In vital applications such as aerospace, automobile, or structural constructions, where safety and toughness are vital, the damaging impacts of porosity on weld top quality can have serious effects, highlighting the significance of reducing porosity through correct welding methods and procedures.
Strategies to Minimize Porosity
To improve the top quality of welded joints and ensure structural integrity, welders and producers use certain methods intended at decreasing the formation of gaps and dental caries within the material during the welding procedure. One effective approach to lessen porosity is to guarantee correct product prep work. This includes complete cleansing of the base metal to eliminate any pollutants such as oil, grease, or dampness that can add to porosity formation. Additionally, making use of the suitable welding specifications, such as the correct important site voltage, current, and travel rate, is crucial in avoiding porosity. Maintaining a consistent arc size and angle throughout welding also helps in reducing the probability of porosity.

In addition, picking the appropriate securing gas and keeping correct gas circulation prices are essential in minimizing porosity. Using the appropriate welding strategy, such as back-stepping or utilizing a weaving movement, can likewise assist disperse heat evenly and reduce the possibilities of porosity formation. Lastly, making certain proper ventilation in the welding atmosphere to remove any potential sources of contamination is crucial for accomplishing porosity-free welds. By carrying out these methods, welders can successfully reduce porosity and generate premium bonded joints.

Advanced Solutions for Porosity Control
Implementing cutting-edge this technologies and cutting-edge approaches plays a critical duty in attaining premium control over porosity in welding processes. Additionally, employing sophisticated welding techniques such as pulsed MIG welding or changed ambience welding can also aid minimize porosity problems.
One more advanced option involves making use of sophisticated welding tools. For example, using devices with integrated features like waveform control and sophisticated source of power can improve weld quality and minimize porosity risks. In addition, the execution of automated welding systems with exact control over criteria can considerably decrease porosity flaws.
Moreover, integrating sophisticated surveillance and assessment innovations such as real-time X-ray imaging or automated ultrasonic testing can assist in spotting porosity early in the welding process, permitting for instant restorative actions. In general, integrating these sophisticated options can greatly enhance porosity control and improve the overall high quality of welded elements.
Final Thought
In final thought, understanding the scientific research behind porosity in welding is essential for welders click here to find out more and makers to create top notch welds - What is Porosity. Advanced services for porosity control can better improve the welding procedure and make certain a solid and trustworthy weld.